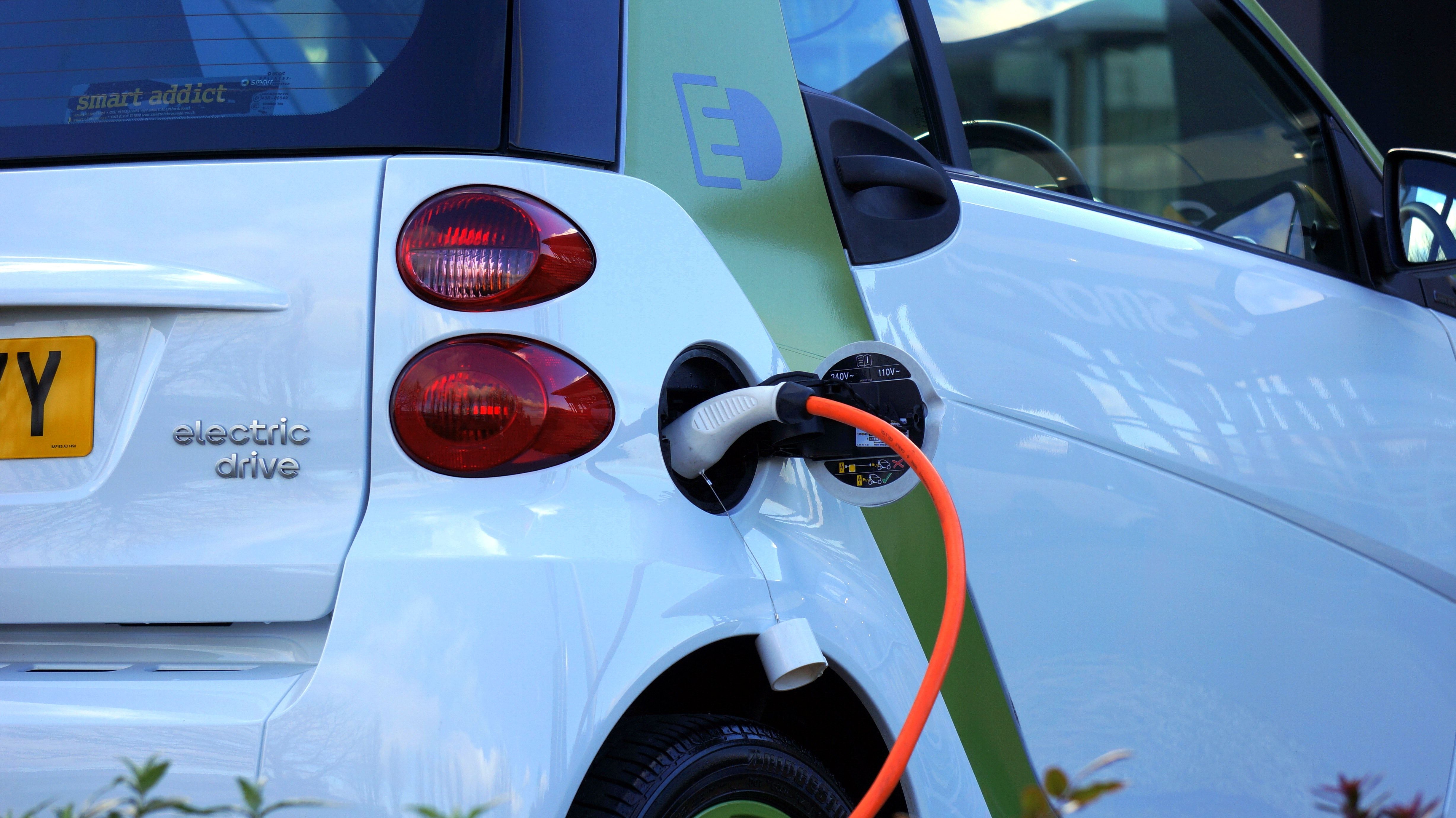
Prices for the silvery white metal – critical to batteries powering the world’s growing fleet of electric vehicles – have surged more than fivefold in the past year, to record levels. While that’s a cost headache for car makers, it’s good news for startups working to recover the materials from spent lithium-ion batteries.
“It’s definitely the time for recycling of lithium-ion batteries,” said Vikrant Singh, chief technology officer and co-founder of BatX Energies, an Indian startup that extracts lithium, cobalt and other materials from spent batteries, and which presented its technology at VivaTech 2022. “Pricing for these materials is increasing, so it’s a very, very highly profitable business.”
While lithium has been notoriously unprofitable to recover from scrap, the price surge has made the metal the most valuable element in most lithium-ion battery chemistries, according to researcher Circular Energy Storage. Until recently, prices for scrap Li-ion batteries were mostly set based on the cobalt and nickel content.
Global sales of electric vehicles more than doubled last year, driving demand for the lithium, cobalt and nickel used to make their batteries. More than 70 countries have set targets for net-zero emissions for 2050, which the International Energy Agency says will require “nothing short of the complete transformation of the global energy system.”
Total corporate funding for battery storage companies rose to 7 billion in 2021 from .6 billion a year earlier, according to Mercom Capital Group. Venture-capital funding for the sector rose to $8.8 billion from $1.6 billion, with most of that money going to lithium-ion battery technology companies.
“Lithium-ion battery demand is growing at its fastest-ever rate and is on course for 50% year-on-year growth,” Simon Moores, CEO of price reporting agency Benchmark Mineral Intelligence, said in a June 23 commentary. “Waiting times for EVs are lengthening, a lithium ion battery shortage is hitting many automakers, and, most crucially, key raw material prices are at all time highs.”
Costly raw materials are great for recycling, prompting companies to put in more effort and investment to make sure valuables aren’t left behind, according to Circular Energy Storage. The market researcher says there was a “huge spike’’ in investment and announcements of new recycling capacity in 2021.
Lithium currently accounts for 18% of the raw-material costs in a lithium-ion battery, ahead of nickel with about 14% and cobalt with 12%, data from Benchmark Mineral Intelligence shows. About 800 grams of lithium carbonate is required per kWh in a lithium-ion battery, according to mining company Savannah Resources, equivalent to about 150 grams of pure lithium. That would mean a 100 kWh battery contains more than $1,000 worth of lithium at today’s prices.
Beyond profitability, the environmental impact of mining battery metals makes recycling critical, said Singh at BatX. “Lithium mining is a water-exhausting activity, cobalt is a very harmful activity in terms of pollution, so it’s our responsibility to create a circular economy by recycling lithium-ion batteries,” the CTO said.
The main methods to recycle batteries either use chemicals to leach out the valuable materials, with recovery rates for lithium and cobalt of more than 99%, or high-temperature smelting, which recovers copper, cobalt, nickel, and turns lithium into slag. New recycling methods are exploring direct physical recycling of battery components.
The European Union has proposed regulation that targets recycling recovery rates for Li-ion batteries of 95% for cobalt and 70% for lithium by 2030, while China has continued to strengthen its rules for battery recycling.
The outlook for mandated recycling efficiency and material-recover rates has focused the attention of battery makers, as well as the commodity giants. Glencore set up a partnership with Canadian recycler Li-Cycle, U.S. startup Ascend Elements in March agreed to recycle battery manufacturing scrap for SK Battery America, while Li-Cycle in April announced an agreement with LG Energy Solutions to do the same.
Carmaker Toyota in June announced a collaboration with Redwood Materials for the recycling of hybrid electric vehicle batteries, and to investigate how to incorporate recycling into Toyota’s battery production in North America.
Recharge, the European industry association for advanced rechargeable and lithium batteries, has cautioned against making requirements for recycled content too strict for European battery makers, saying that will hurt EU plans to set up local production of power cells for the automotive industry.
Battery waste “has reached significant volumes in Asia, making it easier for Asian companies to access recycled battery materials,’’ said Kinga Timaru-Kast, Recharge’s director for public affairs. “Volumes of available secondary raw materials in Europe are low, and a too ambitious recycled content obligation would jeopardize the competitiveness of European batteries.”
Right now, one obstacle recyclers may face is a shortage of used batteries. With expected lifetimes for an electric car battery of ten to 15 years, and the possibility of reusing vehicle batteries for energy storage, recycling will ramp up as the decade progresses, according to McKinsey. Independent recyclers may face a scramble for feedstock in coming years, with availability of end-of-life batteries still limited by the end of the decade, Wood Mackenzie analyst Max Reid predicts
Last year, about 210,000 tons of lithium-ion batteries were available for recycling around the world, and 820,000 tons will be recycled in 2030, Circular Energy Storage estimates.
Recycling could account for 15% to 25% of the metal requirements to produce Li-ion batteries by the end of the decade, according to a report by Avicenne Energy. McKinsey is a little less optimistic, saying lithium recycling could reach around 6% of total supply by 2030, and Wood Mackenzie analyst Max Reid says recycling won’t take off before 2030.
“In the next 10 to 15 years, a recycled content obligation will steepen EU dependency on third country secondary raw materials,” Timaru-Kast at Recharge said. “Too early high recycled content targets might bring shortages of battery raw materials in the EU.”
Yet another challenge includes the variety in designs and chemistry used for lithium-ion batteries. Most Li-ion batteries are not designed to be easily disassembled, and damaged batteries can trigger fires or explosions.
Singh at BatX expects it’ll be another two to three years to start seeing sufficient amounts of electric vehicle scrap. The startup, which is working with companies including Samsung C&T and Hero Electric, will use the time to fine-tune its technology, expand a battery-collection system in India and raise funding for plant expansion, according to the CTO.
“It’s the right time to start, because it will take some time to make it to perfection in terms of circularity and extraction of materials,” Singh said. “We want to preserve these metals for future generations.”
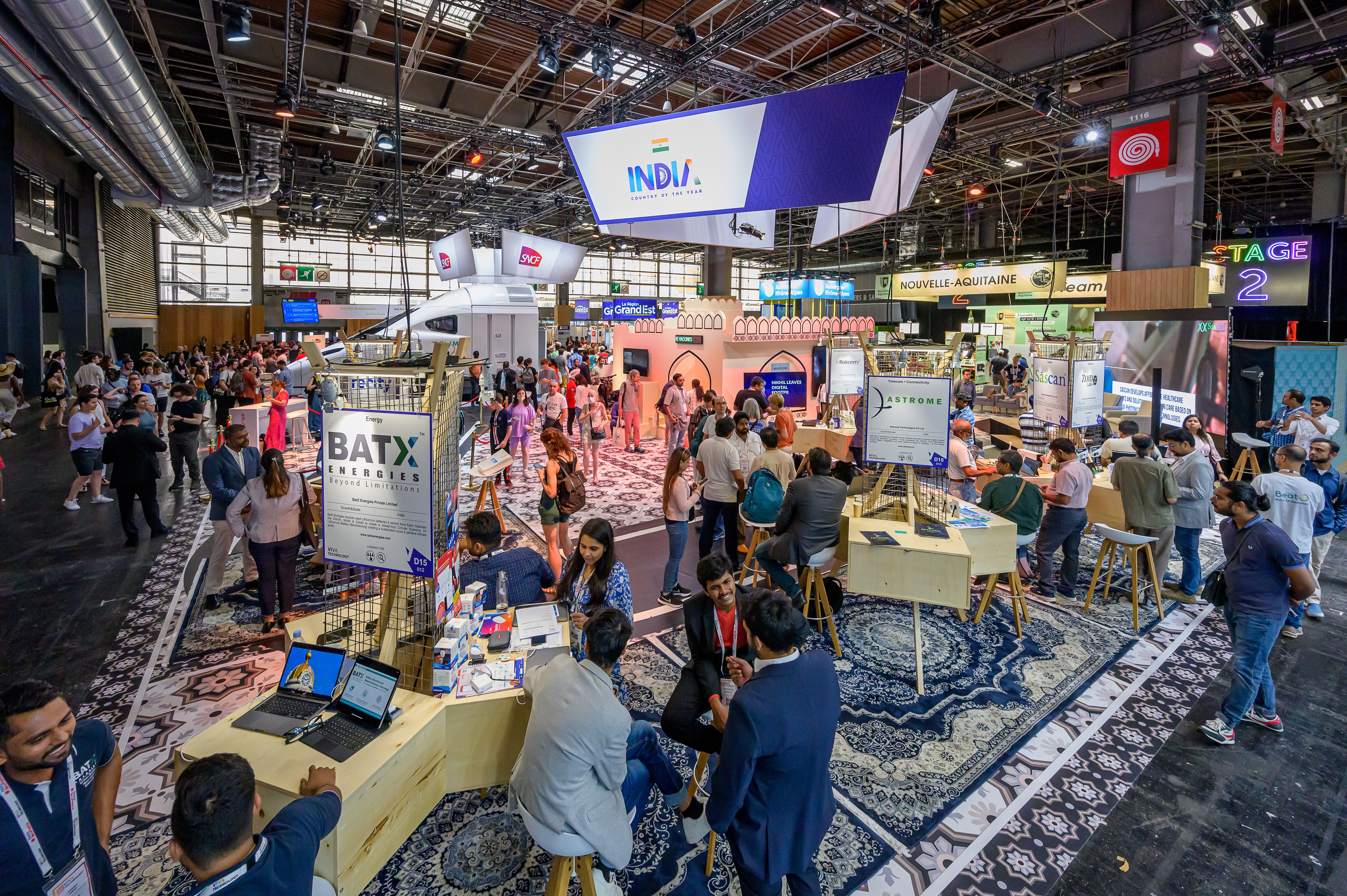
BatX"e;s stand at VivaTech 2022. Photo credit: VivaTech